Cimatron takes the complexity out of cooling system design
Gone are the days when the only safeguard between bad design and production disaster were the keen eyes of moldmakers adept at spotting problems before jobs were sent to the floor.
While the value of experience remains high, today’s advanced software for mold design offers automation and sophisticated analysis functions that go far beyond simply replacing pen and paper to changing the way manufacturers approach the art and science of building molds.
When it comes to designing cooling systems, capabilities that simplify intricate tasks and evaluate mold design in its entirety ensure that waterlines and components are safely and effectively placed, and molds perform as required.
Continuously developed with the needs of the moldmaker in mind, Cimatron’s dedicated technologies for cooling design include tools that help moldmakers of any skill level design with confidence and consistently produce optimal results.
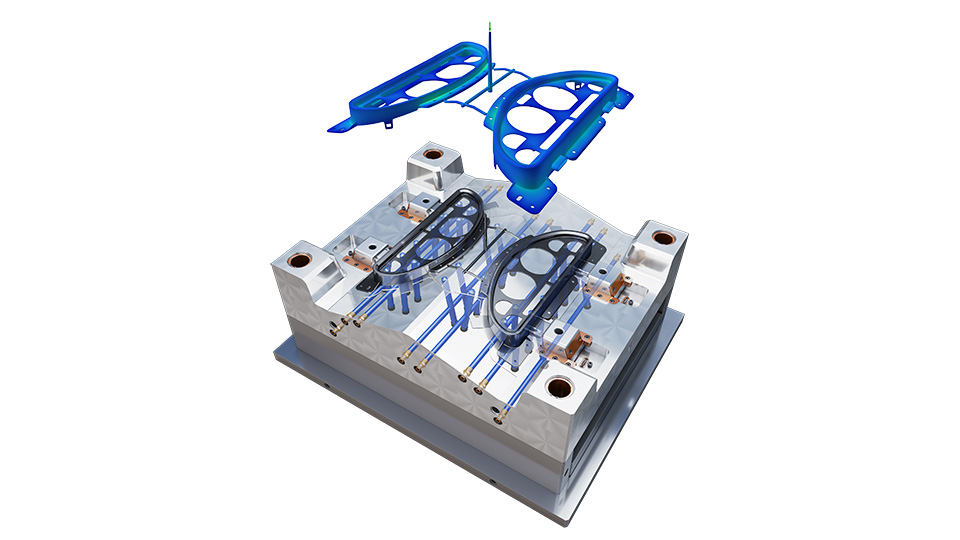
Designing with confidence
Cimatron’s flexible capabilities for cooling system design meet a variety of needs, from fine-tuning waterline positioning to testing whether a design concept will literally hold water.
Two capabilities that simplify both initial and late-stage cooling design are the planar sketching function and the ability to automatically generate waterlines based on the placement of components, such as plugs and connectors.
It takes just seconds to drag and drop a component from a Cimatron component catalog into a design, where waterlines that match the size of the selected component can then be generated with a few mouse clicks. For even more design automation, entire circuits can be created simply by connecting the holes drawn by adding components.
Even when gate and runner design are not yet set in stone — or in steel, as the case may be — designers can quickly gain a general idea of where waterlines should be placed and an understanding of how much space is available. For instance, long holes are often not drilled perfectly straight, but Cimatron’s default clearance parameter will automatically provide enough wiggle room to help designers achieve the results they need regardless of drilling accuracy.
Similarly, Cimatron design tools help prevent performance issues over time by ensuring that waterlines are placed where they will not weaken sections of the mold, especially areas that are repeatedly exposed to alternately high and low temperatures. While Cimatron provides default settings for ideal clearance between design elements, users are provided with the flexibility to set their own parameters.
Simplified baffle design
Cimatron provides several capabilities for the placement of baffles, from calculating ideal length and positioning to supplying, in a convenient table, a list of baffles that need to be ordered from a supplier.
When an initial baffle design is complete, Cimatron can count the baffles and label each with a corresponding hole number on the design. The software will collect all baffle information build a spreadsheet that lists information for each baffle — including the matching hole number on the design, baffle length to be ordered, final baffle length after cutting, and hole size. Having all the information collected in a single easy-to-read format simplifies ordering and prevents production and assembly errors.
Playing it safe
Given the inherent complexity of designing plastic injection molds, software capable of providing an accurate 3D representation of the mold at any step in the design process helps moldmakers visualize design progression. Running checks and analyses to ensure they’re on the right track and verify what their eyes are telling them increases confidence that designs are solid.
Moldmakers can choose to run analysis tools at any point during the design process, such as distance checks that ensure waterlines and components are a safe distance from their neighbors — namely various features and other components — and circuit checks verify the performance of entire circuits.
By analyzing circuits in their entirety, Cimatron can identify sections where poor design is likely to cause problems. For instance, analysis helps designers spot where a plug has been placed in a channel that should be open, where a circuit lacks an output, or where a waterline is divided in two and then comes back together. By assigning specific colors to questionable areas or outright design errors, Cimatron makes it easy to quickly understand problems and ultimately make designs as good as they can be.
For example, color coding based upon specified distances from a hole could let a designer know if the waterline or component has been placed between a designated 200 thousandths (.200) and 250 thousandths (.250) of an inch from the hole.
If the user wants the software to color code the portion of the design that falls between any specified distance parameters, they could choose to “paint” that section red — or any other color they choose — to make it easy to see how close they are to a particular feature or features on either side of the waterline or component they are placing in a design.
Filling analysis and flow simulation
Cimatron’s integration with partner Altair’s Inspire Mold makes it easy for moldmakers with any level of experience to perform simulation throughout development to ensure molds will perform as required. This integration enables designers to seamlessly work back and forth between the two systems to verify design changes seconds after they are made.
Filling analysis and flow simulation tools help moldmakers quickly understand how designs will perform. The ability to verify a design early in the engineering process is especially helpful because it can help designers make improvements that ensure the rest of the design process is more productive.
When mold design is complete, analyses and simulation help designers understand how well the mold will perform and make changes without the need for expensive physical testing. Inspire Mold’s filling analyses and flow simulation capabilities extend to multiple aspects of mold performance, including runner and gate placement, waterline optimization, and analysis of critical factors like cooling efficiency, filling pressure, velocity, and temperature distribution.
Especially helpful is its ability to analyze how mold temperatures affect overall performance, including the prediction of common issues like weld lines and warpage. When problems are identified, the software can generate models of anticipated part deformation. Those models can be shared with Cimatron, where designers can make changes that compensate for the deformation and improved designs simulated in Inspire Mold. This seamless integration supports a workflow between the two systems that improves efficiency and accuracy and helps produce a better product.
Taking the complexity out of cooling
Cimatron automation and tools for cooling system design simplify an inherently complex and error-prone process by empowering moldmakers with any level of experience to design molds that go the distance.
Easy-to-use tools simplify intricate design tasks, while safeguards like distance and analysis checks help designers visualize and resolve problems before they become time consuming and expensive. Flow simulation and filling analysis tools help designers understand how molds will perform at any point in development so that changes made early on will positively impact the rest of the process.
With little room for error and facing increasingly complex demands, today’s moldmakers require reliable technologies to help them meet their goals. When it comes to designing cooling systems, Cimatron helps manufacturers achieve greater productivity, shorten development time, and produce high-quality molds without sacrificing quality.